Tungsten Carbide Blades CVD Coating Process
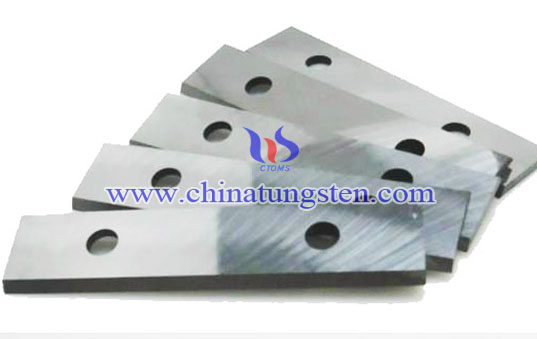
Currently more common coating structure in the tungsten carbide blades CVD coating process is: Titanium nitride - alumina - nitrogen titanium carbide - substrate. Titanium carbide coating has high hardness and wear resistance, oxidation resistance or, when the carbide blade cutting can produce titanium oxide film, reducing the coefficient of friction and reduce tool wear. General carbide blade cutting speed can be increased by 40%, titanium carbide and high bonding temperature, surface grain is fine, carbide blade when cutting steel rarely BUE, suitable for fine cars. Disadvantage is that a coating of titanium carbide and the linear expansion coefficient difference between the substrate larger, fragile decarburized layer formed between the substrate and reduce the bending strength of the tool. Therefore, when heavy cutting or machining a workpiece with a hard material coating inclusions easily crack.
Titanium nitride coating is able to be formed oxide film at a high temperature, good anti-blocking properties can effectively reduce the cutting temperature. Titanium nitride coated blade crater and flank wear ability is stronger than titanium carbide coated inserts. Materials suitable for cutting steel and carbide blade knife stick, surface roughness smaller, higher service life of carbide cutting tools. Besides thermal shock performance of titanium nitride coating is also good, the disadvantage is not as good as with the substrate bonding strength of titanium carbide coating and easy to peel off when the coating is thick .
Coated cemented carbide is the most commonly used method for high temperature chemical vapor deposition method (abbreviated HTCVD method),in the atmospheric pressure or negative pressure deposition system, the pure H2, CH4, N2, TiCl4, AlCl3, CO2 and other gases, or vapors, according to the sediment composition, which will be related to the gas, according to a certain ratio uniformly mixed, turn applied to a certain temperature (usually 1000 ℃ ~ 1050 ℃) of the carbide blade surface, namely the blade surface deposition TiC, TiN , Ti (C, N) or Al2O3, or a composite coating. Using PCVD (plasma chemical vapor deposition) method to coat the surface of cemented carbide inserts has also been applied, the coating process due to the lower temperature (700 ° ~ 800 °), so that the flexural strength of the blade lowered to a lesser extent, for milling insert more appropriate.
Before coating, surface of the blades should be purification, cutting edge parts should be passivated. After coating, due to the presence of coating material differences between the linear expansion coefficient based off the material, it is coated blade surface residual tensile stress inevitably leaving the blade to reduce the bending strength. Generally use a thin layer of TiC coated in surface of the substrate , because the linear expansion coefficient of TiC is close to substrate ; outside apply a TiN, Al2O3 and the like. In the past, single-coating materials use TiC, the double-coating materials use TiC / TiN, TiC / Al2O3, etc., three-coating materials use TiC / Ti (C, N) / TiN, Tic / Al2O3 / TiN and so on. In recent years, with the improvement of the matrix material, the coating material also use TiN as bottom, i.e., TiN / TiC / TiN and other coating materials as well as HfN, MoS2 and the like.