Tungsten Carbide Milling Blades
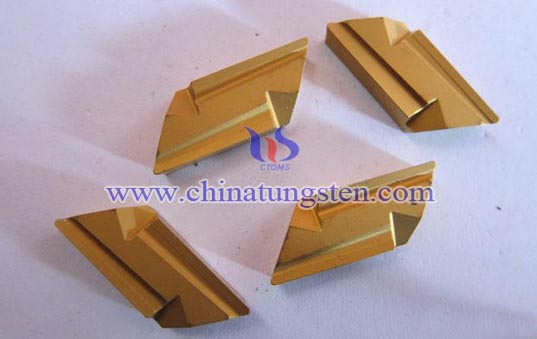
Tungsten carbide milling blades for mechanical processing and manufacturing, according to the processing of different metals (non-metallic) materials and the choice of different materials tungsten carbide milling blades. tungsten carbide milling blades are made of yt14, yt15, yt5, yw1, yw2, yw3, yt05, yg6, yg8 so on.
Tungsten carbide milling blades use should pay attention to the situation:
Cracks appear on the tungsten carbide milling blades, in some cases due to welding stress is too high, exceeding the strength of tungsten steel head generated.
In the welding tools, the height hc blades cutter body should be greater than the height of ht3 times. As hc / ht, after welding, tungsten carbide milling blades easily cause fracture; If hc / ht < 3, tungsten carbide milling blades surface tensile stress, but also prone to cracking; When hc / ht = 4 ~ 5 when the surface tungsten steel head no significant stress, it is difficult to crack, even if cracks were not evident; at hc / ht < 8 when the solder layer to produce uniform load. And bending the first tungsten steel alloy tensile stress along the thickness direction of blades, the strength of the welded layer is greater than the force distribution of the alloy itself is more complex, because it is not joined to the one surface, and two, three or four faces the combination.
In addition, tungsten carbide milling blades rapid heating and rapid cooling, due to the uneven distribution of heat, are likely to generate significant transient stress. In the fast heating,tungsten carbide milling blades Outer compressive stress, the tensile stress in the middle. When the heating rate exceeds the permitted, it may crack or is not visible inside the cracks. When tungsten steel head welding, rapid cooling is also very dangerous, in this case, will appear on the outer tensile stress caused by tungsten carbide milling blades cracks.